Специалист компании "ХимНикель"
Процесс химического никелирования в производстве печатных плат
С развитием на предприятиях Российской Федерации технологий поверхностного монтажа электронных компонентов все большее внимание при изготовлении печатных плат (ПП) уделяется финишным покрытиям, наносимым на различные элементы печатного рисунка. Данные покрытия защищают поверхность медных проводников от окисления и обеспечивают требуемые условия для сварки и пайки электронных компонентов.
Применяемые при производстве ПП защитные покрытия должны обеспечивать:
Производители ПП в РФ, работающие с технологией ENIG, используют, как правило, импортные растворы и оборудование по типовой схеме:
Так, для образования фосфидов никеля содержание фосфора в покрытии никель фосфор должно быть меньше 8% (2). Если фосфора больше, то фосфиды не образуются, а фосфор образует с никелем твердый раствор. Следовательно, и фосфида никеля на поверхности может образоваться не больше 8 %. Если бы дело было в нем, то паяемость ухудшилась бы на такие же 8%, так как фосфид никеля размещен равномерно и в объеме, и на поверхности покрытия. Мы же наблюдаем практически блокировку поверхности.
Известно, что сразу после осаждения покрытие паяется приемлемо. Однако с течением времени способность к пайке теряется и через 6 месяцев сводится к нулю, на что ссылается стандарт IPC-4552(4).
Имеет место также другая гипотеза, которая видит причину черной контактной площадки в коррозии никеля, спровоцированной межкресталитными прослойками. При этом веществом прослойки называется фосфор. Но фосфор в чистом виде в покрытии может существовать только в твердом растворе с никелем. В межкресталитном пространстве, как отдельная фаза, фосфор может присутствовать только в виде интерметаллидов Ni2Р и Ni3P, которые не только не являются причиной зарождения очагов коррозии, но обладают выраженным антикоррозионным действием (1).
При испытании коррозионной стойкости Гутцайт и Мапп обнаружили интересную особенность в поведении покрытия. Появляющиеся на поверхности пятна ржавчины на распространяются по поверхности даже при длительной выдержке образца в коррозионной среде. А значит, механизм распространения коррозии от центров зарождения в случае химического никелирования не соответствует действительности (1).
Если наше предположение об оксидной пленке является верным, то в образцах со свежим покрытием количественный анализ не должен показать сколько-нибудь значимое присутствие кислорода. Тогда как в образцах, пролежавших несколько месяцев, кислород должен присутствовать количественно. И без защитного слоя золота процесс потемнения покрытия должен занять гораздо меньше 6 месяцев.
Для подтверждения гипотезы было покрыто 28 медных образцов из электролита химического никелирования (ГОСТ 9.303-84), 4 из которых подверглись рентгенофлуоресцентному анализу (РФА) сразу после покрытия, и далее анализировались по 4 образца каждые две недели.
РФА является элементным анализом. Он не показывает наличия того или иного соединения, но позволяет качественно обнаружить и количественно определить элементный состав вещества.
В таблице приведены результаты анализа.
Применяемые при производстве ПП защитные покрытия должны обеспечивать:
- хорошую смачиваемость припоем поверхности;
- сохранение способности к пайке и сварке длительное время (до 6 месяцев);
- сохранение прочности пайки и сварки в процессе эксплуатации готового изделия.
- HASL - процесс горячего облуживания плат с последующим выравниванием расплава струями горячего воздуха;
- ENIG – процесс нанесения на медную фольгу подслоя из химического никеля (~ 4 – 5 мкм) и, поверх него, слоя тонкой пленки иммерсионного золота (~ 0,05 – 0,2 мкм);
- ImSn - процесс покрытия иммерсионным оловом.
Данная статья посвящена технологии нанесения защитного ENIG покрытия на ПП.
Производители ПП в РФ, работающие с технологией ENIG, используют, как правило, импортные растворы и оборудование по типовой схеме:
- Кислая очистка заготовки ПП
- Микротравление
- Активация
- Химическое осаждение никеля
- Иммерсионное золочение
- Низкая адгезия покрытия никель-фосфор к медной подложке, когда паяное соединение отрывается по границе медь — никель. Чаще всего низкая адгезия связана с некачественной обработкой поверхности или недостаточной ее промывкой после предшествующих химическому никелированию операций;
- Плохая смачиваемость припоем поверхности покрытия никель-фосфор и ухудшение этой характеристики со временем из-за изменения свойств поверхности. Внешне поверхность темнеет, из-за чего явление получило название «черный никель» или «черная контактная площадка» (3).
Мы считаем данный механизм маловероятным.
Так, для образования фосфидов никеля содержание фосфора в покрытии никель фосфор должно быть меньше 8% (2). Если фосфора больше, то фосфиды не образуются, а фосфор образует с никелем твердый раствор. Следовательно, и фосфида никеля на поверхности может образоваться не больше 8 %. Если бы дело было в нем, то паяемость ухудшилась бы на такие же 8%, так как фосфид никеля размещен равномерно и в объеме, и на поверхности покрытия. Мы же наблюдаем практически блокировку поверхности.
Известно, что сразу после осаждения покрытие паяется приемлемо. Однако с течением времени способность к пайке теряется и через 6 месяцев сводится к нулю, на что ссылается стандарт IPC-4552(4).
Из чего следует, что, либо фосфид никеля образуется не сразу при осаждении и за 6 месяцев две твердые фазы (никель и фосфор) каким-то образом вступают в реакцию, либо фосфид никеля образуется сразу при осаждении. Но тогда он должен целенаправленно диффундировать из объема покрытия к поверхности и полностью перекрыть ее. Энергия активации реакции образования фосфида никеля довольно высокая. На практике фосфид никеля в покрытии образуется при температуре не менее 300˚С. То есть, при температуре хранения, это невозможно. А его диффузия невозможна термодинамически, так как положение на поверхности покрытия не является энергетически более выгодным, чем в объеме.
***
Имеет место также другая гипотеза, которая видит причину черной контактной площадки в коррозии никеля, спровоцированной межкресталитными прослойками. При этом веществом прослойки называется фосфор. Но фосфор в чистом виде в покрытии может существовать только в твердом растворе с никелем. В межкресталитном пространстве, как отдельная фаза, фосфор может присутствовать только в виде интерметаллидов Ni2Р и Ni3P, которые не только не являются причиной зарождения очагов коррозии, но обладают выраженным антикоррозионным действием (1).
При испытании коррозионной стойкости Гутцайт и Мапп обнаружили интересную особенность в поведении покрытия. Появляющиеся на поверхности пятна ржавчины на распространяются по поверхности даже при длительной выдержке образца в коррозионной среде. А значит, механизм распространения коррозии от центров зарождения в случае химического никелирования не соответствует действительности (1).
На наш взгляд, потемнение покрытия и ухудшение его паяемости связано с тем, что на поверхности образуется оксид никеля, который и препятствует смачиваемости поверхности припоем, и, как следствие, пайке. Но окисление происходит равномерно по всей поверхности по причине его микрокристаллической структуры при малом (меньше 8%) содержании фосфора. И то, что паяемость ухудшается со временем, говорит в пользу именно этого механизма. Что касается защитного золотого покрытия, то хорошо известно свойство газов диффундировать в металлы.
Например, диффузия водорода в металлы (наводораживание) - распространенный побочный эффект электрохимического никелирования, приводящий к хрупкости стали подложки. Таким образом, монослой золота, которым никель защищен от воздействия среды, серьезным препятствием не является, хотя и замедляет процесс окисления.
Если наше предположение об оксидной пленке является верным, то в образцах со свежим покрытием количественный анализ не должен показать сколько-нибудь значимое присутствие кислорода. Тогда как в образцах, пролежавших несколько месяцев, кислород должен присутствовать количественно. И без защитного слоя золота процесс потемнения покрытия должен занять гораздо меньше 6 месяцев.
Для подтверждения гипотезы было покрыто 28 медных образцов из электролита химического никелирования (ГОСТ 9.303-84), 4 из которых подверглись рентгенофлуоресцентному анализу (РФА) сразу после покрытия, и далее анализировались по 4 образца каждые две недели.
РФА является элементным анализом. Он не показывает наличия того или иного соединения, но позволяет качественно обнаружить и количественно определить элементный состав вещества.
В таблице приведены результаты анализа.

В первой партии образцов кислород практически отсутствует. Тогда как в остальных партиях кислород присутствует количественно и его содержание увеличивается с течением времени. А значит, поверхность подвергается окислению.
После проведенного исследования наша задача свелась к выбору электролита химического никелирования, который позволяет осаждать сплав никель — фосфор минимально подверженный окислению. Известно, что наиболее высокая коррозионная стойкость покрытия никель фосфор достигается, когда оно аморфно. То есть, не обладает кристаллической структурой, и, стало быть, малейшей разностью потенциалов поверхности. Окисления никеля не происходит, так как на изопотенциальной поверхности отсутствует электрохимическая предпосылка коррозии.
Фосфор в покрытии никель-фосфор является аморфизатором, но в строго определенном интервале концентраций: от 8% до 16%. Значит, требовался электролит обеспечивающий покрытие с содержанием фосфора от 8% до 16 % и поддерживающий это соотношение на всем протяжении эксплуатации.
Это позволило отсеять растворы химического никелирования в ТИ к которым указывалось другое содержание фосфора. Не подходили и такие, где интервал содержания фосфора проходил через 8% (например, от 5% до 9%), так как с каждой корректировкой такого раствора содержание фосфора в покрытии падает. И если первые ПП паяются нормально, то последующие (после снижения фосфора меньше 8%) окисляются все быстрее и смачиваемость поверхности падает.
Учитывались также технологические характеристики электролитов химического никелирования, а именно:
После проведенного исследования наша задача свелась к выбору электролита химического никелирования, который позволяет осаждать сплав никель — фосфор минимально подверженный окислению. Известно, что наиболее высокая коррозионная стойкость покрытия никель фосфор достигается, когда оно аморфно. То есть, не обладает кристаллической структурой, и, стало быть, малейшей разностью потенциалов поверхности. Окисления никеля не происходит, так как на изопотенциальной поверхности отсутствует электрохимическая предпосылка коррозии.
Фосфор в покрытии никель-фосфор является аморфизатором, но в строго определенном интервале концентраций: от 8% до 16%. Значит, требовался электролит обеспечивающий покрытие с содержанием фосфора от 8% до 16 % и поддерживающий это соотношение на всем протяжении эксплуатации.
Это позволило отсеять растворы химического никелирования в ТИ к которым указывалось другое содержание фосфора. Не подходили и такие, где интервал содержания фосфора проходил через 8% (например, от 5% до 9%), так как с каждой корректировкой такого раствора содержание фосфора в покрытии падает. И если первые ПП паяются нормально, то последующие (после снижения фосфора меньше 8%) окисляются все быстрее и смачиваемость поверхности падает.
Учитывались также технологические характеристики электролитов химического никелирования, а именно:
- срок службы до замены (он оценивался в количестве никеля, осаждаемого из 1 литра раствора с учетом корректировок);
- стабильность раствора (электролит должен быть устойчив к перегреву, и не допускать реакцию в объеме, «саморазряд» или «шлам»);
- обладать технологически приемлемой скоростью (не менее 20-25 мкм/час).
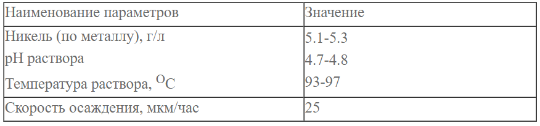
Была покрыта опытная партия ПП, которые, в течение полугода с интервалом в месяц проходили испытания на паяемость и подвергались рентгенофлуоресцентному анализу (РФА).
С течением времени ухудшение паяемости не происходило. РФА определил 10% содержание фосфора в покрытии и не показал увеличение количества кислорода на поверхности, что подтвердило нашу гипотезу об окислении никелевого покрытия с содержанием фосфора меньше 8% и его резистентности к окислению при содержании фосфора больше 8%.
Адгезионные свойства покрытия определялись испытанием на отрыв с помощью скотча. Ни на одном из образцов отрыва по границе медь-никель не наблюдалось.
В процессе внедрения и эксплуатации электролит НСА-10 показал следующие параметры:
С течением времени ухудшение паяемости не происходило. РФА определил 10% содержание фосфора в покрытии и не показал увеличение количества кислорода на поверхности, что подтвердило нашу гипотезу об окислении никелевого покрытия с содержанием фосфора меньше 8% и его резистентности к окислению при содержании фосфора больше 8%.
Адгезионные свойства покрытия определялись испытанием на отрыв с помощью скотча. Ни на одном из образцов отрыва по границе медь-никель не наблюдалось.
В процессе внедрения и эксплуатации электролит НСА-10 показал следующие параметры:
- устойчивое содержание фосфора 10% ± 0,25% в покрытии;
- скорость осаждения 25 мкм/час (при 950С);
- высокую стабильность раствора, вплоть до температуры его кипения;
- длительный срок службы (осаждение из 1 литра раствора до 30 гр. никеля, что соответствует 30 загрузкам);
- возможность корректировки раствора по площади покрываемой поверхности, т.е. без анализа состава раствора.
Библиография
- Горбунова К.М., «Физико-химические основы процесса химического никелирования», Наука, 1964 г.
- Шалкаускас М.И., Вашкялис А.И., «Химическая металлизация пластмасс». 3-е издание, перераб. – Л.: Химия, 1985. – 144 с.
- SaM Pepe. Tech tips… Black Pad/Empfasis – October, 2007.
- Финишные покрытия печатных плат, Элинформ, 2007 (http://www.elinform.ru/articles_68.htm)